Mastering Injection Mold Manufacture: The Key to Success in Metal Fabrication
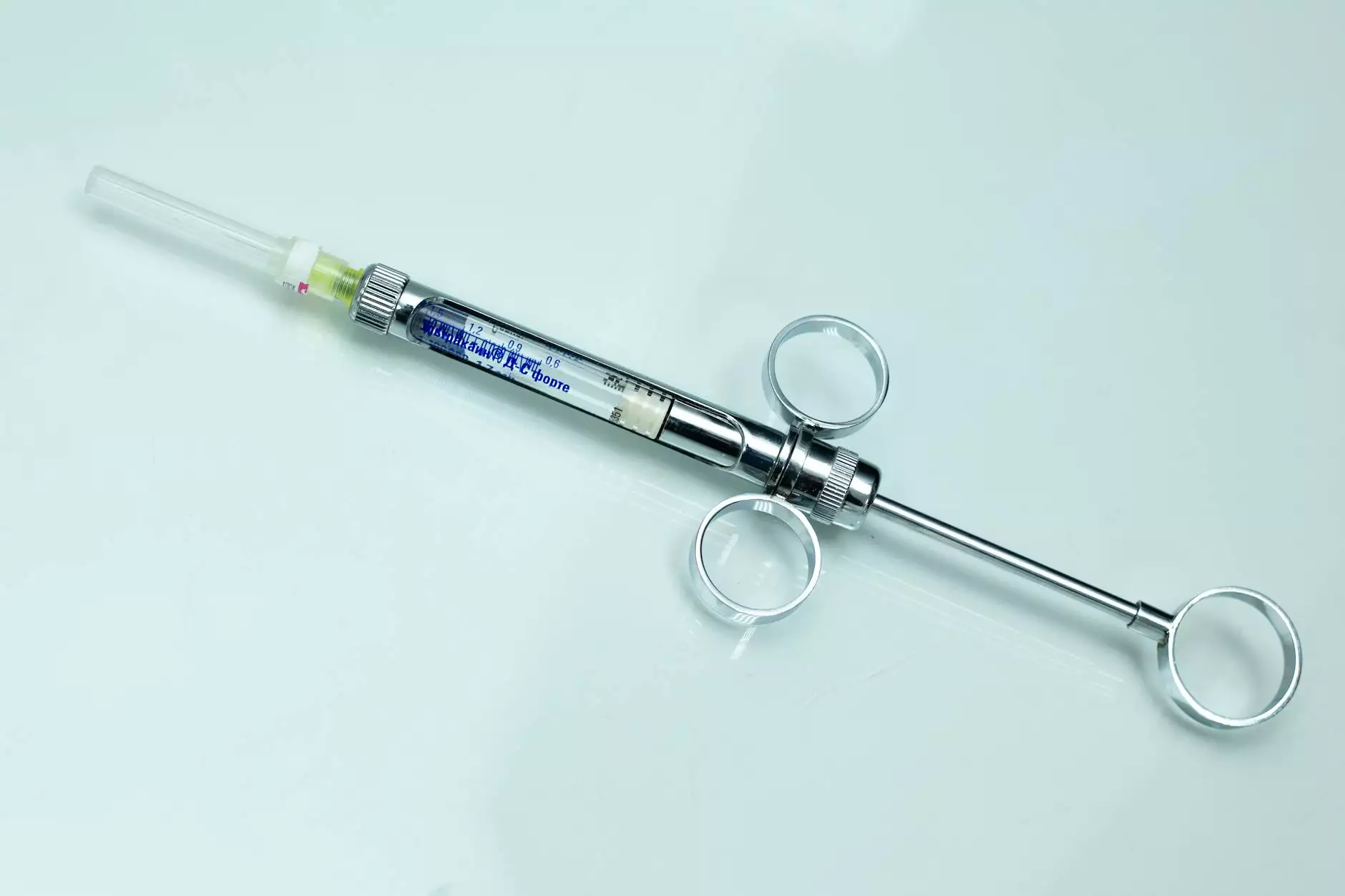
In today's rapidly evolving industrial landscape, the significance of injection mold manufacture cannot be overstated. As industries ranging from automotive to consumer goods continuously seek to innovate and enhance efficiency, injection molding has emerged as a vital process in the realm of metal fabrication. This comprehensive guide aims to delve deep into the intricacies of injection mold manufacturing, its advantages, the application sectors, and how businesses can harness its power to achieve their goals.
Understanding Injection Mold Manufacture
Injection mold manufacture is a sophisticated manufacturing process that involves injecting molten material into a pre-designed mold. This process is predominantly used for producing parts in high volumes with outstanding precision and repeatability. The materials used in this process can vary, but most commonly involve metals and plastics, enabling a diverse range of applications suitable for various industries.
The Process of Injection Molding
The injection molding process encompasses several critical stages:
- Material Selection: Choosing the appropriate material is the first step that influences the quality and feature of the end product.
- Mold Design: Engaging skilled professionals in mold design ensures the production of intricate and functional parts.
- Injection Process: The molten material is injected into the mold cavity under pressure to take its shape.
- Cooling: Post-injection, the molded part is cooled to gain strength and stability.
- Demolding: Once cooled, the part is ejected from the mold, ready for further processing or finishing.
The Advantages of Injection Molding in Metal Fabrication
Embracing injection mold manufacture can yield numerous benefits for businesses engaged in metal fabrication. Here are some of the most notable advantages:
1. Cost-Effectiveness
Beyond the initial investment in mold design and creation, injection molding is a highly efficient process. Once the mold is manufactured, producing parts is relatively inexpensive, particularly when scaled to high volumes. This economy of scale is a driving factor for companies looking to maximize profitability.
2. High Precision and Consistency
Injection molding produces parts with remarkable precision. The exactness of the molds allows for uniform parts that meet stringent specifications, making it an ideal choice for industries like automotive, aerospace, and medical devices where quality and reliability are non-negotiable.
3. Versatility of Materials
Though often associated with plastics, injection molding can be utilized with various materials, including metals and alloys. This versatility supports diverse applications, allowing businesses the flexibility to innovate without being limited by material constraints.
4. Reduced Waste
Compared to other manufacturing techniques, injection molding generates significantly less waste due to its efficient material usage. This not only contributes to sustainability efforts but also enhances the overall efficiency of production processes.
5. Complex Geometries and Features
Another remarkable advantage of injection mold manufacture lies in its ability to achieve complex shapes that would be challenging or impossible with traditional machining methods. Features such as undercuts, threads, and intricate designs can be incorporated directly into the mold, streamlining the manufacturing process.
Applications of Injection Molding Across Industries
The versatility of injection molding enables its application across various industries, including:
1. Automotive Industry
The automotive sector relies heavily on injection molding for producing components such as dashboards, panels, and housing for electrical systems. The precision and durability offered by injection molded parts are critical for vehicle safety and functionality.
2. Consumer Goods
From kitchenware to electronic devices, many consumer goods utilize injection molded components. The ability to produce items in bulk ensures that manufacturers can meet consumer demand while maintaining affordability.
3. Medical Devices
In the medical field, the need for sterile, high-precision components makes injection molding indispensable. From surgical instruments to prosthetics, the accuracy and quality assurance of injection molded parts are vital.
4. Aerospace
Aerospace components often require high-strength materials and precise tolerances. Injection molding meets these demanding criteria, playing a crucial role in manufacturing lightweight yet durable parts for aircraft.
Choosing the Right Injection Mold Manufacturer
1. Expertise and Experience
Look for manufacturers with a proven track record in injection mold manufacture. Evaluate their portfolio to ensure they have successfully handled projects similar to yours.
2. Advanced Technology
Modern injection molding relies on sophisticated technology. Ensure that your manufacturer utilizes up-to-date machinery and software for design and production to maintain high standards.
3. Quality Assurance Practices
Inquire about the quality control measures the manufacturer employs. A reliable partner should have robust processes in place to ensure that every part meets required specifications.
4. Customization Capabilities
Your manufacturing partner should be able to accommodate design changes and offer customization to meet your specific needs, ensuring flexibility throughout the project lifecycle.
5. Customer Support and Collaboration
Effective communication and collaboration are essential in manufacturing partnerships. Ensure your chosen manufacturer values customer relations and is responsive to inquiries and needs.
Future Trends in Injection Mold Manufacturing
As industries evolve, so does the landscape of injection molding. Here are some anticipated trends that could shape the future of injection mold manufacture:
1. Emphasis on Sustainability
With increasing pressures to adopt sustainable practices, the injection molding sector is likely to focus on eco-friendly materials and processes. Manufacturers are exploring biodegradable plastics and minimizing waste generated during production.
2. Integration of Advanced Technologies
Technological advancements such as automation, IoT, and 3D printing are increasingly being integrated with traditional injection molding processes. These innovations promise to enhance production efficiency and reduce lead times.
3. Customization and Personalization
With customers seeking tailored products, the ability to customize injection molded parts will be crucial. The industry may see a shift towards more flexible manufacturing systems that accommodate quick changes and personal specifications.
4. Enhanced Collaboration with Clients
As competition intensifies, manufacturers might engage more closely with clients during the design and production phases, fostering partnerships that lead to better product outcomes.
Conclusion
Injection mold manufacturing plays a pivotal role in the world of metal fabrication, offering unparalleled benefits in terms of efficiency, precision, and versatility. By understanding the process, its advantages, and the significant applications across various industries, businesses can harness the full potential of injection molding to propel their growth.
Choosing the right manufacturing partner is a critical step in leveraging this technology effectively. As the industry embraces new technologies and sustainable practices, the future of injection mold manufacture looks bright and full of opportunities for innovation.
Whether you are in the automotive, consumer goods, medical, or aerospace sectors, the impact of high-quality, precision-engineered injection molded parts cannot be overlooked. Stay ahead of the curve, and explore the transformative benefits of injection molding for your business today!