The Impact and Importance of Pressure Die Casting Dies Manufacturers
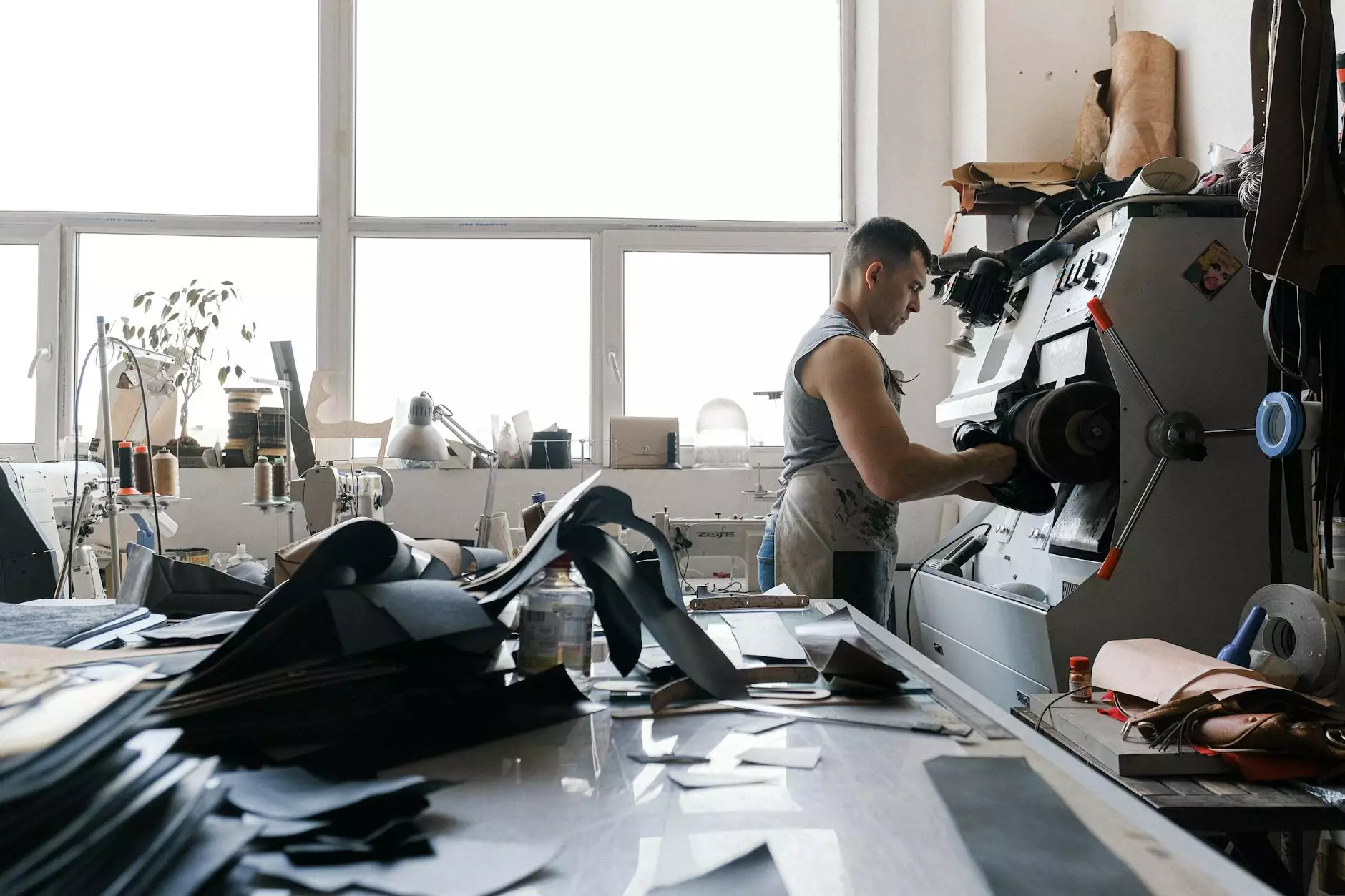
In today's competitive industrial landscape, pressure die casting dies manufacturers play a pivotal role in the production of high-quality metal components. From automotive parts to intricate electronics housings, the demand for precision-engineered components has never been higher. Understanding the importance of these manufacturers is crucial for businesses looking to optimize their production processes and enhance their product offerings.
What is Pressure Die Casting?
Pressure die casting is a manufacturing process that involves forcing molten metal into a mold cavity under high pressure. This method offers numerous advantages over traditional casting techniques, making it a favored choice in various industries. The high pressure facilitates the creation of components with intricate designs and superior surface finishes. Key benefits of pressure die casting include:
- High Dimensional Accuracy: Components produced via pressure die casting maintain tight tolerances.
- Excellent Surface Finish: The process results in smooth surfaces, reducing the need for secondary finishing.
- Rapid Production Rates: High-speed operations minimize cycle times, ideal for mass production.
The Role of Manufacturers in the Die Casting Process
Pressure die casting dies manufacturers are integral to the efficiency of the die casting process. They design and produce the molds used for casting that directly influence the quality of the finished products. The bespoke nature of die manufacturing requires a high level of expertise and technical knowledge, ensuring that each die is tailored to specific production needs.
Designing High-Quality Dies
The design phase is critical to the effectiveness of any pressure die casting operation. Skilled manufacturers use advanced software and technologies, including CAD (Computer-Aided Design), to create intricate die designs. This phase includes elements such as:
- Material Selection: Choosing suitable materials for the dies, such as steel alloys that can withstand high temperatures and pressures.
- Thermal Management: Designing cooling channels in the die to optimize the cooling rates and minimize cycle time.
- Release Mechanisms: Incorporating effective release systems to prevent casting defects.
Manufacturing Process
The manufacturing of pressure die casting dies involves several steps, each requiring precision and expertise. Common processes include:
- Machining: Using CNC machines to sculpt the die from solid blocks of metal.
- Heat Treating: Enhancing the mechanical properties of the die material to increase durability.
- Polishing: Creating a smooth surface finish on the dies to improve the quality of the castings.
Benefits of Collaborating with Expert Die Manufacturers
Partnering with experienced pressure die casting dies manufacturers offers numerous benefits for businesses. These manufacturers can significantly impact production efficiency and product quality:
Expert Guidance and Support
Mature manufacturers bring years of experience to the table, providing valuable insights and recommendations that can optimize production processes. Their expertise ensures that:
- The design is fully optimized for the intended application.
- Potential pitfalls in the casting process are identified and addressed early.
- Future production scalability is accounted for in the design phase.
And Reduced Costs
By utilizing high-quality dies, businesses can minimize defects and waste, therefore reducing overall production costs. Here, long-term benefits distinctly outweigh initial costs, offering:
- Lower Scrap Rates: Better design leads to fewer scrapped components.
- Reduced Downtime: Quality dies minimize the risk of machine failures.
- Consistent Output Quality: High-quality dies ensure uniformity across large production runs.
Applications of Pressure Die Casting
Pressure die casting is utilized across a wide array of industries. Here, we delve into some of the most prominent applications:
Automotive Industry
The automotive sector is one of the largest consumers of pressure die-cast components. Die casting enables the production of lightweight yet strong parts, crucial for enhancing fuel efficiency and reducing emissions. Commonly produced parts include:
- Engine blocks
- Transmission housings
- Structural components and brackets
Consumer Electronics
The demand for sleek and compact designs in consumer electronics has led to an increase in the use of die-cast parts. These components are often found in:
- Laptop casings
- Smartphone housings
- Television frames
Aerospace Industry
In aerospace, where strength-to-weight ratios are critical, pressure die casting is leveraged to produce components that can withstand harsh environments while remaining lightweight.
Choosing the Right Manufacturer of Pressure Die Casting Dies
Finding the right partner among pressure die casting dies manufacturers can significantly influence your operational success. Here are key factors to consider when selecting a manufacturer:
Reputation and Experience
Search for manufacturers with a proven track record. Their past performance can give you insight into their reliability and capability. Look for:
- Years of operation in the industry
- Customer testimonials and case studies
- A portfolio of related projects
Advanced Technology and Equipment
Modern manufacturing equipment, supported by up-to-date technology, allows for better precision and efficiency. Ensure the manufacturer uses:
- CNC machining tools
- CAD and CAM software for die design
- High-tech inspection tools for quality assurance
Custom Solutions
Every project is unique, and a capable manufacturer should offer tailored solutions that meet your specific needs. Discuss with potential partners their ability to:
- Design custom die solutions
- Adapt production variations based on product evolution
- Maintain flexibility in production schedules
Future Trends in Pressure Die Casting
As industries evolve, so does the technology behind pressure die casting. Current trends shaping the future include:
Automation and Smart Manufacturing
With the rise of Industry 4.0, automation is becoming a critical component of die casting processes. This shift allows for:
- Increased efficiency and output
- Enhanced monitoring and predictive maintenance
- Reduced labor costs
Sustainability Practices
The metal fabrication industry is increasingly focusing on sustainability. Manufacturers are seeking methods to reduce their environmental footprint by:
- Implementing recycling strategies for scrap metals
- Adopting eco-friendly die materials
- Optimizing energy consumption in production processes
Advancements in Material Science
New alloys and composite materials are being developed that enhance the attributes of die-cast components, leading to lighter, stronger, and more durable products that can withstand extreme conditions.
Conclusion
The role of pressure die casting dies manufacturers is essential in the modern manufacturing landscape. By understanding this sector's intricacies and leveraging high-quality die solutions, businesses can achieve greater operational efficiency, product quality, and innovative designs. As technology advances and industries evolve, the partnership with skilled manufacturers will remain key to maintaining a competitive edge in the market. For businesses looking to ensure their production processes are optimized, partnering with a reputable manufacturer like DeepMould.net could pave the way to future success.