The Ultimate Guide to Precision Hardware Parts in Metal Fabrication
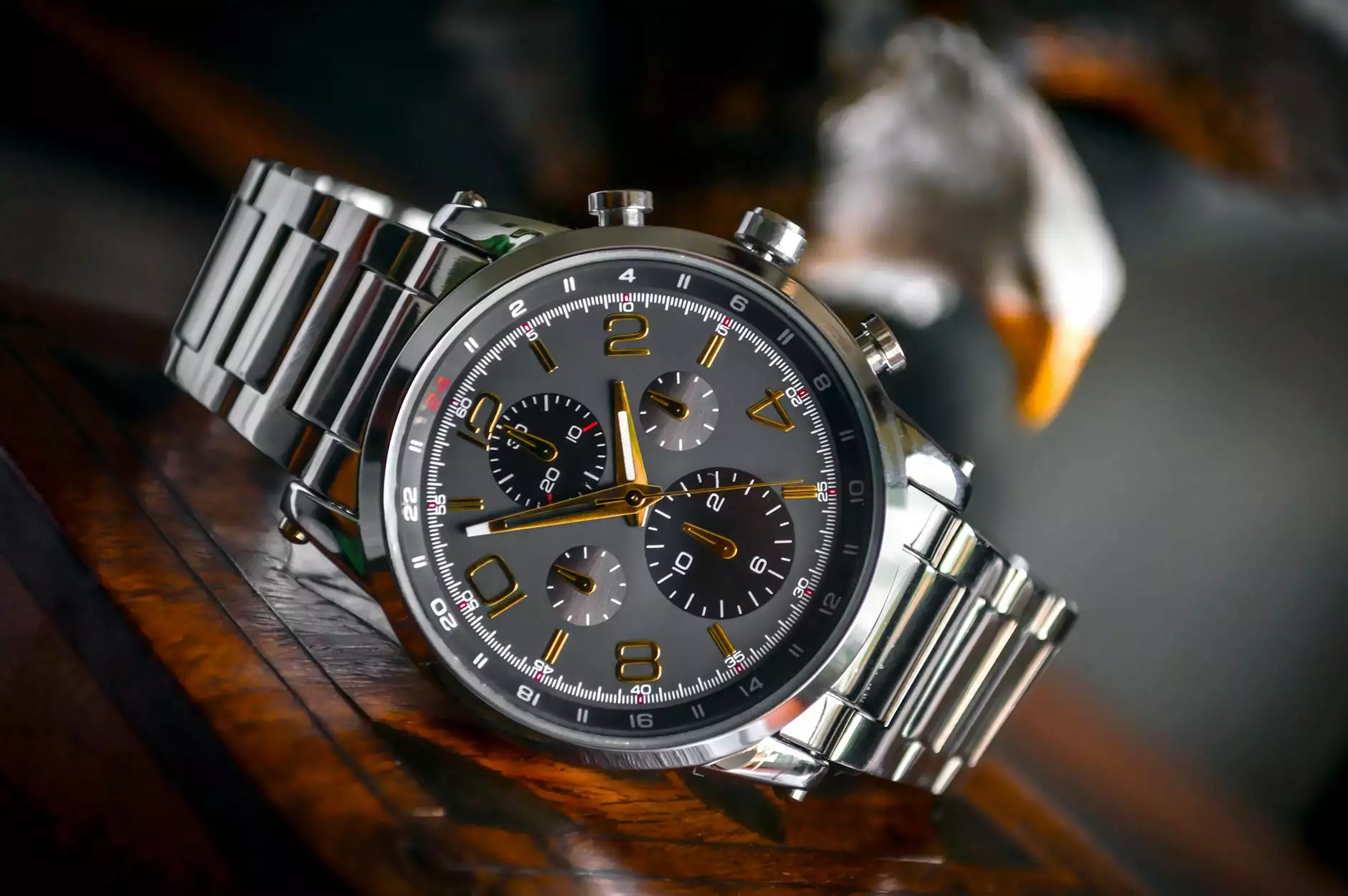
Precision hardware parts play an essential role in the world of metal fabrication. As industries continuously seek perfection in their engineering processes, the demand for precision components has skyrocketed. At deepmould.net, we recognize the significance of these components in creating high-quality products that meet and exceed customer expectations. In this comprehensive guide, we will delve into the various aspects of precision hardware parts, their applications, and how they are manufactured, all while emphasizing their relevance in today’s dynamic business landscape.
Understanding Precision Hardware Parts
At its core, precision hardware parts refer to components manufactured to extremely tight tolerances, ensuring that they fit perfectly and function seamlessly within machines or assemblies. These parts are crucial in ensuring the reliability and longevity of various mechanisms. There are a variety of industries where precision hardware parts are indispensable, including automotive, aerospace, medical, and consumer electronics.
The Importance of Precision in Manufacturing
In manufacturing, the term "precision" relates to the degree of accuracy and repeatability that can be achieved. Here are several reasons why precision is vital:
- Quality Assurance: Products that utilize precision hardware parts are generally more consistent and of higher quality.
- Efficiency: Machinery operating with precisely engineered parts tends to run smoother, thereby reducing downtime and maintenance costs.
- Safety: In many industries, precision hardware parts are essential to ensure the safe operation of critical systems.
- Cost Reduction: Precision contributes to minimizing waste during the manufacturing process, leading to reduced costs.
Key Applications of Precision Hardware Parts
The utility of precision hardware parts spans across numerous domains. Here are some applications categorized by industry:
1. Automotive Industry
In the automotive sector, precision hardware parts are used in engines, transmissions, and various structural components. For instance, components like cylinders, valves, and gearbox components must meet stringent specifications to ensure optimal vehicle performance and safety.
2. Aerospace Sector
The aerospace industry requires precision parts for everything from structural frames to control systems. Components such as turbines and landing gear assemblies demand the utmost precision due to their critical functioning and the environments in which they operate.
3. Medical Equipment Manufacturing
In medical applications, precision is not just preferred, it is mandatory. Components in devices like infusion pumps, surgical instruments, and diagnostic machinery must operate flawlessly to ensure patient safety and effective treatment.
4. Consumer Electronics
Precision parts are also prevalent in consumer electronics, enabling devices to operate effectively in increasingly compact sizes. High-performance products like smartphones, tablets, and computers contain numerous precision components that affect their overall function and durability.
Manufacturing Process of Precision Hardware Parts
Creating precision hardware parts involves a series of meticulous steps. The following outlines the typical manufacturing process:
1. Design and Prototyping
The manufacturing of precision hardware parts begins with detailed designs and prototypes. Using advanced CAD (Computer-Aided Design) software, engineers create 3D models and simulations to ensure that the parts will meet the required specifications.
2. Material Selection
Choosing the right materials is paramount in precision manufacturing. Common materials include:
- Aluminum: Lightweight and corrosion-resistant, suitable for various applications.
- Stainless Steel: Known for its durability and resistance to rust, often used in medical devices.
- Titanium: Exceptional strength-to-weight ratio, frequently seen in aerospace components.
3. Machining
Machining processes such as CNC milling, turning, and electrical discharge machining (EDM) are employed to shape and cut materials into the desired configurations. CNC technology allows manufacturers to achieve high levels of precision through robotic automation, significantly reducing human error.
4. Surface Finishing
After the initial machining, the parts often undergo surface finishing processes to enhance their functional characteristics. This can include:
- Polishing: To create a smooth finish.
- Anodizing: To improve corrosion resistance.
- Coating: For enhanced durability and aesthetic appeal.
5. Quality Control
All precision manufactured parts undergo rigorous quality control checks to ensure they meet stringent industry standards. This can involve dimensional analysis, mechanical testing, and non-destructive testing to validate integrity and performance.
Advantages of Using Precision Hardware Parts
The benefits of incorporating precision hardware parts into manufacturing processes are numerous:
- Enhanced Performance: Products with precision components operate more effectively, providing better performance and reliability.
- Longer Longevity: Well-made precision parts tend to have a longer functional lifespan, leading to reduced replacement costs.
- Market Competitiveness: Companies that utilize precision hardware can produce superior products, helping them stand out in a crowded market.
- Sustainability: Efficient production processes using precision parts can lead to decreased waste and more sustainable manufacturing practices.
Future Trends in Precision Hardware Manufacturing
The landscape of manufacturing precision hardware parts is continually evolving. Some future trends that are shaping the industry include:
1. Automation and Robotics
As manufacturers look to improve efficiency, automation and robotics will play an increasingly critical role. Robots can perform repetitive machining tasks with unfaltering precision, reducing costs while increasing production speed.
2. 3D Printing
3D printing technology is revolutionizing the way precision parts are manufactured. This innovative approach allows for the creation of complex geometries that are challenging or impossible to produce through traditional methods, while also reducing material waste.
3. Advanced Materials
Development in materials science is leading to the evolution of new alloys and composites that can perform better and withstand extreme conditions. These materials will be fundamental in the innovation of precision hardware parts.
4. Industry 4.0
The advent of Industry 4.0, characterized by smart manufacturing and IoT (Internet of Things), will allow manufacturers to gather real-time data, enabling better decision-making and operational efficiency, which is particularly advantageous in precision engineering.
Conclusion
In the realm of metal fabrication, precision hardware parts are not just components; they are the backbone of quality production and operational success. By utilizing state-of-the-art manufacturing processes and continuously innovating, businesses can ensure they remain at the forefront of their industries. At deepmould.net, we are committed to delivering high-quality precision hardware parts tailored to fit the needs of various sectors. As the demand for precision continues to grow, staying informed and adaptable will be key to thriving in this competitive landscape.