Maximizing Efficiency and Innovation with Rapid Prototype Injection Molding
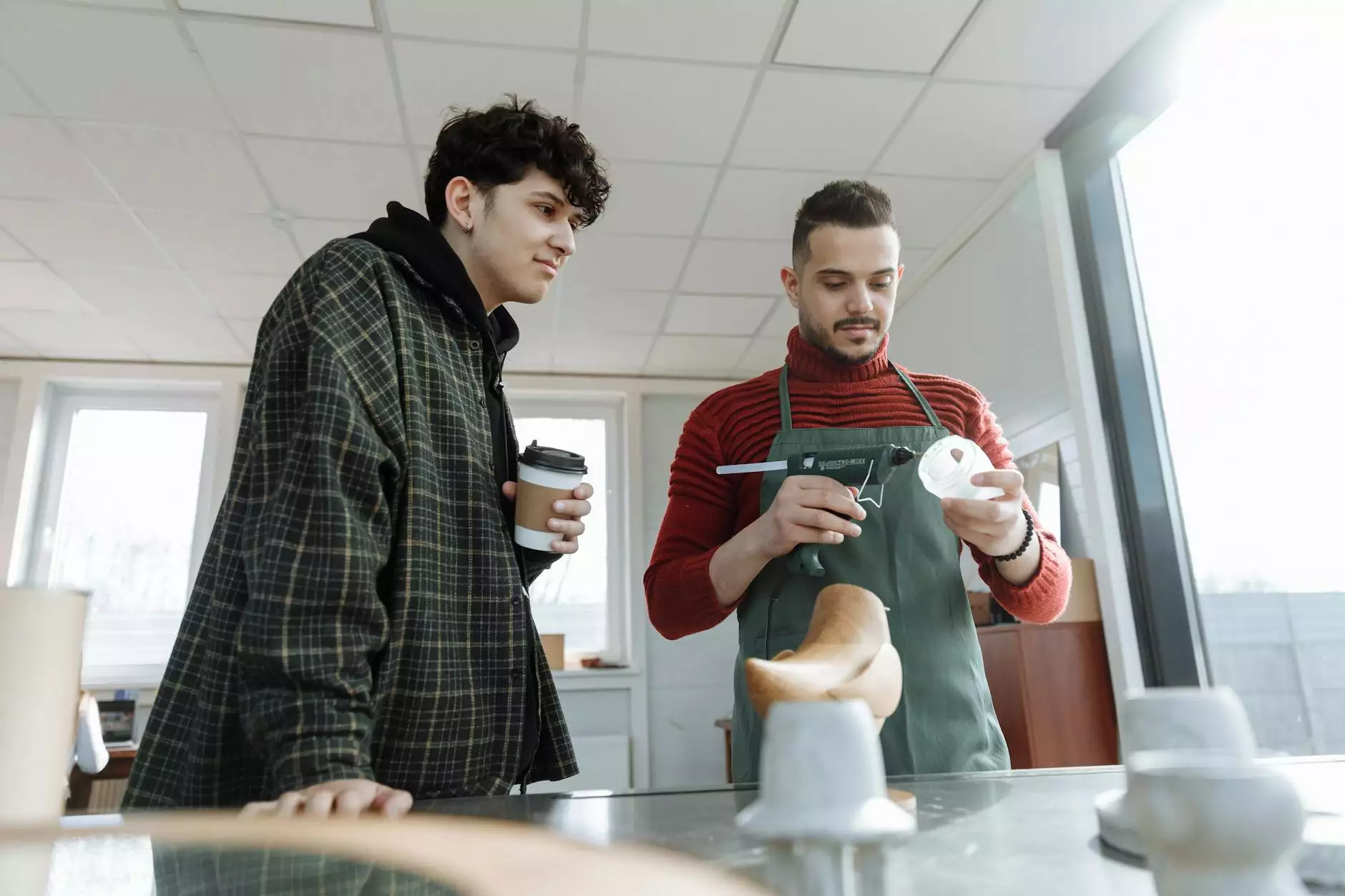
In today's fast-paced world, where technological advancements occur at lightning speed, businesses are always looking for innovative methods to enhance their manufacturing processes. One area that has seen significant growth and efficacy is rapid prototype injection molding. This method not only streamlines production times but also significantly reduces costs while maintaining the highest quality standards.
Understanding Rapid Prototype Injection Molding
Rapid prototype injection molding is an advanced manufacturing process that allows designers to create prototypes swiftly and effectively. The process involves the use of injection molding techniques with rapid prototyping technologies, enabling manufacturers to produce high-quality, functional prototypes in a fraction of the time it would traditionally take.
How Rapid Prototype Injection Molding Works
The fundamental principle of rapid prototype injection molding relies on the creation of a mold that can be filled with molten material. Here’s a brief overview of the process:
- Design Phase: Using CAD software, engineers draft detailed designs that can be easily manipulated for tweaks and adjustments.
- Mold Creation: A mold is created using computer numerical control (CNC) machining or 3D printing technologies.
- Material Selection: Various thermoplastics can be utilized, depending on the desired properties of the final product.
- Injection Process: The material is heated and injected into the mold, where it cools and solidifies.
- Prototype Finishing: The prototype is removed from the mold, and any necessary finishing touches are applied.
Benefits of Using Rapid Prototype Injection Molding
The benefits of rapid prototype injection molding are extensive, making it an essential tool for businesses in various industries. Here are some of the key advantages:
1. Speed to Market
One of the most significant advantages is the reduced time frames for developing and bringing products to market. By utilizing rapid prototyping techniques, businesses can quickly test concepts and iteratively improve designs, significantly speeding up the overall development timeline.
2. Cost Efficiency
Reducing the time to product launch directly correlates with cost savings. Shortened development cycles mean decreased labor costs and lower expenditure on materials, making rapid prototype injection molding a financially smart choice for businesses.
3. Enhanced Design Quality
Moreover, the ability to create high-fidelity prototypes allows for thorough testing and validation of designs before mass production. This comprehensive testing phase facilitates the identification of potential design flaws early in the process, allowing for adjustments that enhance overall product quality.
4. Flexibility in Design
The iterative nature of rapid prototype injection molding means that designers have the flexibility to make changes and optimizations as the prototype is being developed. This adaptability is crucial in industries where consumer preferences shift rapidly or where technological advancements frequently change design requirements.
5. Comprehensive Material Options
With access to a wide range of materials, businesses can select options that best suit their product requirements, whether it be for durability, aesthetics, or functionality.
Applications of Rapid Prototype Injection Molding
Rapid prototype injection molding finds its applications across multiple sectors including:
- Automotive Industry: Used for designing and testing various components, streamlining the development of vehicles.
- Consumer Electronics: Essential for housing and shell prototypes to ensure perfect fit and function.
- Medical Devices: Critical for prototype production where precision and compliance with safety regulations are paramount.
- Aerospace: Engaging in rapid prototyping to reduce costs while meeting stringent safety standards.